�A study of
Osmotic Distillation.
Miles Rzecho=
wicz
and Richard M. Pashley*.
University of New South Wales, Australian Defence
Force Academy, Canberra, Australia. E-mail: [email protected]
Graphical Abstract:
Figure 1. Schematic representation of water penetration int=
o a
hydrophobic pore, within a hydrophobic membrane. The liquid water (phase A) will not readily enter a vapour-fi=
lled
pore or channel (phase B) in a hydrophobic material, such as Teflon or
polypropylene, due to the high water contact angle, θ, on the hydrophobic surface.� Although liquid water will not enter th=
e fine
hydrophobic porous network, water vapour will easily pass through the pores,
into dry air or a vacuum.
The Laplace equation (1) gives the pressure differ=
ence
(D=
P) across any
curved fluid interface:
<=
![endif]>��������������������������������������������������������������� =
(1)�������������������������������������������������=
����������������� ���� (1)
where g is the surface tension of the liquid and r is the radius of curvature of the
water-air interface, which is usually assumed to be spherical.� If rc
is the radius of a capillary tube or pore, it follows from simple geometry
(again assuming that the meniscus is spherical and that q>900) that the radius of the meniscus, r, is given by:
����� <=
![endif]>�������������������������������������������������=
������������ (2)������������������������������������������������=
���������������������������������������������������������������������������=
��������������
and hence t=
he
Laplace pressure (positive by definition) is given by the equation (for q >900):
�<=
![endif]>����������� ���������������������������������������� (3)������������������������������������������������=
��������������������������������������������������������������������������
This
is the minimum pressure required to force liquid water into the pores, where
the pore walls have a water contact angle of q.
One industrial application of the Laplace pressure
generated in a pore is the use of porous Goretex (i.e. Teflon) or polypropylene membranes to remove dissolved gas=
es
from water down to the ppb range2,3.
This process depends on the Laplace pressure preventing water flow i=
nto
the hydrophobic pores. On one side=
of
the membrane is water and on the other a vacuum. As can be seen from the Laplace equatio=
n, as
long as the water contact angle remains high, say at around 1100,
the pressure required to push water into the pores is greater than 1 atm (s=
ee
Fig. 2). The Laplace pressures generated in a hydrophobic membrane depend on
the water contact angle on the membrane surface, as illustrated in Figure 2=
.
Thus, the Laplace pressure generated across a curv=
ed
meniscus (as shown in Fig. 1, between points A and B) in a Teflon pore of 1=
mm diameter is about 1atm4.�
Pores of this size (or less) will therefore allow the pressure in the
water to be at 1atm, with a vacuum,� or
water vapour (at a pressure of about 20mm of Hg at 200C) on the
other side, without allowing liquid water to flow through the pores.� This method works because water has a h=
igh
surface tension (73mJm-2) and Teflon has a very low tension (of
about 18mJm-2).� The
water-Teflon interfacial tension is also high at about 45mJm-2 a=
nd
hence the water contact angle on Teflon is very high, at about 1100.
Teflon and polypropylene porous membranes are al=
so
used commercially to concentrate wine and fruit juice for export5,6.
These processes are referred to as membrane distillation and osmotic
distillation (OD)7.� In =
each
of these processes, the solution to be concentrated is flowed around the
exteriors of porous hollow fibres of these materials, while a vapour pressu=
re
gradient is used to draw vapour from the solution into the interiors of the
fibres.� In the case of membrane
distillation, this is achieved either by applying a vacuum to the fibre
interiors, or by circulating through them a solvent at a lower temperature =
than
that of the feed solution.� In the =
case
of osmotic distillation, concentrated brine is used as the low vapour press=
ure
fluid.� In these processes it is
important that the high contact angle be maintained and so the membranes are
regularly washed to prevent adsorption of surface active agents.
�The
concentrative effect of osmotic distillation occurs due to the effect of
solutes on the chemical potential of the water.�
For ideal mixtures, the chemical potential of the water depends upon=
the
mole fraction of water in the solution, according to the relation:
<=
![endif]>�� =
���=
����������� (4)��������������������������������������
where <=
![endif]> and
<=
![endif]> are the
chemical potentials of water in the solution and in the pure state,
respectively, and
<=
![endif]> is the mo=
le
fraction of water in the solution. At
equilibrium, the vapour phase chemical potential
<=
![endif]>must be equal to
<=
![endif]>and for an ideal system Raoult’s law relates the
reduced vapour pressure to the mole fraction of water in the solution:
<=
![endif]>������������������������������������=
������������������������������ (5)��������� ������������������������������������������������=
������������������������������������������������������������������
where <=
![endif]> and
<=
![endif]>
A pressure gradient can therefore be created betwe=
en
two solutions with the same solvent, but with different, non-volatile, solu=
te
concentrations. If two such soluti=
ons
are kept separate, but their vapours are allowed to mix, the chemical poten=
tial
difference will drive net vapour transfer to dilute the more concentrated
solution. This process will continue until equilibrium is reached, which ma=
y occur
when the chemical potential of the solvents is equalized by, say, a tempera=
ture
differential, convergence of solution concentrations, or a combination of b=
oth.
This process may be accelerated by the use of thin, porous hydrophobic
membranes to separate the liquids, but allowing the passage of vapour. The use of a membrane can lead to the p=
rocess
occurring over a very large surface area, increasing the rate at which the
vapour is transferred.
The process of osmosis is also driven by differenc=
es
in water chemical potentials across a membrane.
The osmotic pressure of a solution, is equal to the pressure which m=
ust
be applied to prevent net flow from a pure water reservoir into the solution
via a semi-permeable membrane. The
change in chemical potential of water caused by applying a pressure is give=
n by
the relation:
<=
![endif]>��� (6)����������������������� ������������������������������������������������=
�������
where <=
![endif]>�is the molar volume of wate=
r, P
is the standard pressure and Π is the
additional, applied (osmotic) pressure.�
Using equation (4) and equating the change in chemical potential cau=
sed
by the applied pressure with the change produced by adding solute, gives the
relationship:
<=
![endif]>�
(7)
assuming that the solvent is incompressible.� For dilute solutions <=
![endif]> can be
approximated as -
<=
![endif]> , the mol=
e fraction
of solute, which, in turn, allows us to replace
<=
![endif]> with
<=
![endif]> , where <=
/span>
<=
![endif]> is the nu=
mber
of moles of solute, and V is the
volume of solvent. Applying these
approximations leads to the well known van’t Hoff equation:
�
<=
![endif]>��������������������������������� (8)��������� ���������=
���������������������������������� ������������������������������������������������
where Π is the osmo=
tic
pressure, V is the water (solve=
nt)
volume and nS is the
number of moles of solute.� Applying
Raoult's law to equation (7), we obtain the result:
<=
![endif]>��������������������������������������� (9)
This relationship demonstrates that the osmotic
pressure can be calculated directly from vapour pressure measurements.
In an alternative approach, it can be shown that t=
his
correlation arises due to the Kelvin effect, where the curvature of the
interface affects the vapour pressure of the liquid, according to the Kelvin
equation:
<=
![endif]>������������������������������������=
������������� (10)�������������������������������������������������=
������������������������������� ������������������������������������������������=
����������������������������
In the case of a salt solution, where the vapour pressure has been
depressed according to Raoult's law, it may be increased back to its normal
value by creating an interface with a positive radius of curvature,
�������������� <=
![endif]>������������������������������������������� (11) =
=
The curvature of the interface creates a Laplace pressure, and hence
according to equation (1):
<=
![endif]>������������������������������������=
������������������ (12)�������������������������������������������������=
������������������������������� �������������� ������������������������������������������������=
����������������
which leads us back to the van't Hoff equation, (9), demonstrating t=
hat
the hydraulic pressure applied to the concentrated phase required to equali=
se the
vapour pressures of the two phases is identical to the osmotic pressure.
These equations contain several approximations and
assumptions which causes the theoretical predictions of both the vapour and
osmotic pressures of solutions to deviate significantly from real values, at
high solute concentrations. Liquid=
s are
slightly compressible, and also the molar volume of the pure solvent is not=
the
same as that of the solvent in a solution. Further, the replacement of <=
![endif]> with
<=
![endif]> is an
approximation, and the vapour phases, at higher pressures, may not behave
ideally. However, for simple, dilu=
te
solutions, these approximations do not produce significant errors. Another limitation is introduced by Rao=
ult's
law which predicts the reduction of water vapour pressure, up to solution
concentrations of about 2M NaCl. B=
eyond
this concentration, the difference between the Raoult's law prediction and =
the
experimental measurements8 becomes considerable, reaching about =
25%
at the limit of solubility (see Fig. 3).
Figure 3. This graph shows the measured8 and ide=
al9
vapour pressure differences between pure water and varying NaCl solution
concentrations, at 200C. The depression in vapour pressure predi=
cted
using Raoult's law is linear, whereas the experimental data shows non-linear
behaviour.
At higher concentrations, the water mole fraction =
must
be replaced with the activity of the water, <=
![endif]> thus:
<=
![endif]>���=
� �������������� (13)��������������������� �����������=
�������������������������������� ��������������������������������������������� =
span>
Activities can be obtained directly from the
measurement of vapour pressures, using the relation
�� <=
![endif]> <=
span
style=3D'mso-tab-count:4'> =
(14) =
=
=
Most of the data in the literature on osmotic pres=
sure
is given in terms of the ‘Practical Osmotic Coefficient’ f,10 which is defined as:
<=
![endif]>
<=
![endif]> <=
/span>(16) =
=
(Note that aw
=3D xw for ideal mix=
tures). Now, since the osmotic pressure is give=
n by:
<=
![endif]> (17) =
=
where V
<=
![endif]>
<=
![endif]>
However, even this result is subject to
approximations. The introduction o=
f the
activity of the water corrects for the non-ideal behaviour of the
solution. It is still assumed, tho=
ugh,
that the vapour phase behaves ideally.
This is true to a very close approximation, under normal circumstanc=
es,
where the vapour pressure is low. =
Under
circumstances where the vapour pressure increases significantly, for exampl=
e,
at higher temperatures, or for very volatile solvents, it may become necess=
ary
to replace the pressure of the gas phase with the fugacity. However, this correction was not necess=
ary
under the circumstances of these experiments, since the vapour pressure of
water at room temperature is low.
1.2. Limits =
of
Conventional Methods of Determining Solution Osmotic Pressures
Equation (9) can be used to calculate the osmotic
pressure of a solution from the measured vapour pressures10. However, this equation requires values =
for
the molar volume of the water, or the partial molar volumes, for
solutions. The partial molar volum=
es of
water in concentrated salt solutions are not easily measured, and so for the
purposes of such measurements it is usually assumed to be equivalent to the
pure water molar volume. This
approximation is often used in published osmotic pressure data9,10,11<=
/sup>.
While the vapour pressure of the solution can be accurately measured, publi=
shed
osmotic pressure values, or their analogues (e.g. practical osmotic
coefficients), include this error.
However, by independently and directly measuring the vapour pressure=
s of
solutions, and their corresponding osmotic pressures, it would be possible =
to
calculate the partial molar volume of water in concentrated salt solutions.=
Whilst vapour pressures can be measured accurately,
measuring osmotic pressures directly is more difficult. Osmotic membranes, such as those used in
reverse osmosis, do not totally exclude solutes. When used for seawater desalination,
typically up to 5% of the salt passes through the membrane, instead of being
excluded. Even new, high-quality
membranes allow up to 1% of dissolved salt to cross the membrane12,13<=
/sup>. As a result, a system that uses RO memb=
ranes
to measure osmotic pressures will not produce accurate results. An alternative method would be to use v=
apour
phase transfer across a hydrophobic membrane. Transfer through the vapour p=
hase
should effectively eliminate unwanted solute transfer, allowing a direct
pressure measurement that can then be compared with vapour pressure
measurements, to calculate the partial molar volume of the solvent, at that
concentration. It is expected that=
the
partial molar volume will have a small impact on osmotic pressure calculati=
ons,
of the order of about 2%, even for the most concentrated salt solutions14. However, the lack of availability of pa=
rtial
molar volume data leaves some uncertainty.
Apparent molar volumes of salts are usually estimated assuming that
water has a constant partial molar volume15.
2.� Methods and Materials
A solution of AR grade sodium chloride (Merck) in
laboratory deionised water was recirculated through the interiors (lumensid=
e)
of the hollow fibres in a Liquicel 2.5x8 Extraflow hollow fibre cartridge
(Membrana, Charlotte NC, USA), with X40 fibres (polypropylene fibres with 2=
5%
porosity). A 100mL measuring cylinder was used as a reservoir to contain the
excess solution, and to monitor the change in volume of the solution. Purified water was likewise circulated =
around
the exteriors (shellside) of the hollow fibres.
The flow rate of both liquids was equal, and was controlled and
maintained at 50mL per minute, using a small peristaltic pump. The hollow fibre cartridge was position=
ed
below the reservoirs, in order to exclude air, as far as possible, by keepi=
ng the
liquids under a positive hydrostatic pressure.
This arrangement was designed to force any entrapped air out through=
the
hollow fibre walls. This configura=
tion
is illustrated in Fig. 4.
The volume of the liquids in the reservoirs was
recorded every 15 minutes, for 1 hour and 15 minutes per run, before both
liquids were drained from the apparatus and replaced. The conductivity of the liquids was rec=
orded,
at the beginning and the end of each run, with a Radiometer CDM210 4-pole
conductivity probe. This was to en=
sure
that there was no mixing of the liquids due to damage to the membrane, or
faulty tubing, etc. Sodium chloride
solutions were used, at concentrations of 0.1, 0.5, 1, 2, 3, 4 and 4.5 M. The experiment was repeated until at le=
ast
four stable, consistent and reproducible results were recorded, for each
concentration. The hollow fibres w=
ere
also tested for leakage, using a Liquicel MiniModule, 1.7x5.5 hollow fibre
cartridge, with X50 fibres (polypropylene fibres with 40% porosity). The cartridge was fed, as above, with 1M
NaCl, and purified water. The puri=
fied
water was dyed with methylene blue dye (Aldrich). No trace of dye was visible in the salt
solution, even after several hours of fluid flow.
Figure 4. Schematic diagram of the experimental apparatus u=
sed
in this study. The apparatus consisted of a peristaltic pump, which drew
solutions from two measuring cylinders, at equal flow rates, circulated them
through the hollow-fibre cartridge, and returned them to their respective
cylinders.� One cylinder contained
de-ionised water, which was passed over the hollow-fibre exteriors (shellsi=
de),
while the other contained aqueous NaCl solutions, of various concentrations=
, which
was passed through the fibre interiors (lumenside).� The transfer of water through the membr=
ane
was measured by observing the solution levels in the measuring cylinders.
The vapour pressure of solutions is dependent upon=
the
temperature, and therefore the vapour transfer rate may be expected to vary
significantly with substantial temperature variations in the feed
solution. The proportional differences between the vapour pressures of
the concentrated and dilute solutions will remain constant at different
temperatures, and therefore the rate of transfer may be expected to increas=
e at
higher temperatures, where the liquid vapour pressures are higher, and the
absolute vapour pressure difference is greater. Likewise, a lower
temperature may be expected to retard the process. All of the
experimental osmotic distillation measurements reported here were carried o=
ut
in a climate-controlled room, at 21-23oC.
In all of the osmotic distillation experiments, the
volume of the salt solution was observed to increase steadily, whilst the
volume of water reduced by a corresponding amount. The conductivity of the liquids indicat=
ed
that there was no detectable liquid leakage across the membrane. The relationship between the average ho=
urly
flow rate and the concentration of the salt solution was found to be non-li=
near
and increased with concentration difference. The averaged results, from many
osmotic distillation experiments, carried out at room temperature, are
summarized in Fig. 5. All of the data obtained at high concentrations fell
within 20% of the overall average flux rates given in Fig. 5. In these transfer flux experiments, car=
eful
flushing was required when salt solutions were changed to different
concentrations, to obtain consistent membrane transfer rates. Care was also required in the exclusion=
of
air from the system, especially following solution changes.
Figure 5. Experimentally measured flow rates across the hol=
low
fibre membranes, from pure water into salt solutions, as a function of the =
salt
concentration. The experimental results are compared with the ideal, linear
prediction from Raoult�s law. The experimentally measured rate of transfer =
of
water vapour, by osmotic distillation, was found to vary with solution
concentration in a non-linear manner.�
The measured flux follows a greater than proportional relationship w=
ith
the concentration difference between the dilute and concentrated feed
solutions.� The shape of this curve=
is
very similar to that of the published experimental vapour pressure data, as
shown in Fig. 3.
The conductivity of the pure water never exceeded
16µScm-1, and never changed significantly over the course of an
experiment. This indicates that at=
no
point were significant amounts of salt present in the pure phase, and that =
any
salts that were present in the pure phase were not transferred by leakage, =
over
the course of an experiment, but rather by trace contamination during the s=
etup
of each new experiment. The use of=
a
dyed solution in a similar cartridge also indicated that there was no direct
liquid transfer through the membrane.
These results can be used to predict the size of
installation needed to treat water at a given rate, based only on the
concentration difference between the two aqueous solutions. The total area of the hollow fibres ins=
ide
the cartridge, based on the manufacturer's specifications, was 1.4m<=
span
lang=3DEN-AU style=3D'font-size:10.0pt;font-family:"Times New Roman","serif=
";
mso-ansi-language:EN-AU'>², with a porosity of 25%. Assuming that concentrated reject brine=
from
a reverse osmosis process is used as a feed, and low salt waste as the dilu=
te
solution, a concentration difference of about 1M is expected. At this concentration difference, the
observed flow rate was found to be about 4mL of water transferred, per m² of
membrane, per hour. If an installa=
tion
was required to dilute the concentrated reject stream to half of its origin=
al
level, this would yield a 2x higher product flow rate.
4.� Analysis and Discussion
4.1. Compari=
son
of Observed Transfer Rate with Industrial Membrane Processes
For a concentration difference of 2M NaCl,
corresponding to an osmotic pressure of about 100atm, an observed OD flow r=
ate
of about 9mL per m² per hour was observed.
By comparison, a forward osmosis system, using the same concentratio=
n of
NaCl and distilled water as feeds, produces flow rates of about 20 litres p=
er m2
per hour16. Much of this
difference can be accounted for by the different densities of the fluid bei=
ng
transferred across the membranes. =
For
example, 1cm3 of liquid water corresponds to about 1g of water,
while 1cm3 of water vapour, at a vapour pressure of about 23 mba=
r (i.e. water vapour pressure at 20°C=
),
represents about 17µg of water vapour.
Hence, the transfer of water as a vapour is intrinsically slow. The hydrophobic membranes are also 80 m=
icrons
thick, as opposed to an active layer of 0.2 microns, or less, for commercial
reverse osmosis membranes, further reducing the thermodynamic drive of the
vapour transfer process.
The rate of flux of the OD process can be increase=
d by
increasing the cross flow rate, adjusting the liquid temperatures, and by
increasing the concentration difference between the feed solutions. Increasing the cross flow rate, either =
by
increasing the liquid feed rate, or by stirring, will reduce the formation =
of
concentration gradients and boundary layers.
Increasing the concentration difference will increase the vapour
pressure difference. Increasing the
temperatures of both solutions will increase the water vapour pressures and
will therefore increase transfer flux rates.
Increasing the temperature of the dilute solution more than the
concentrated solution will increase the vapour pressure difference driving =
the
process. This process is then refe=
rred
to as membrane distillation, or membrane osmotic distillation, rather than
osmotic distillation, in acknowledgement of the fact that the difference in
vapour pressures is created by thermal means, rather than by osmotic pressu=
re
differences.
Using a higher cross flow rate, and a greater
concentration difference between the feed solutions, flux rates of about 14=
0mL
per m2 per hour have been recorded experimentally17, =
in a
system similar to that used here.
Further gains may be made by using higher porosity membranes (40%
porosity membranes are commercially available), more efficient membrane
packaging and engineering to maximise the use of the available membrane sur=
face
area, and minimising entrapped air. The surface area of a membrane, for a given size of
membrane cartridge, may be increased by use of alternative geometries, such=
as
spiral winding, compared with the hollow fibres used here. Optimising OD
membrane processes has produced fluxes as high as 1-6L per m2 pe=
r hr18. A useful comparison of the productivity of the OD
system is with the rate of productivity per unit of membrane area of a reve=
rse
osmosis system, which are specified commercially as producing up to 500L pe=
r m2
per hr12. This hi=
gh
flux is because reverse osmosis is driven by an applied pressure up to 35atm
greater than the osmotic pressure, in the liquid phase, whereas the evapora=
tive
processes used in OD are driven by a pressure difference, in the vapour pha=
se,
of only a few percent of the vapour pressure, itself a small fraction of one
atmosphere. It should be noted that although OD has a lower flux rate, the
process also has a significantly lower energy consumption, compared to SWRO=
.
Based on these results, an osmotic distillation
system, used to pre-treat feedwater for a reverse osmosis process, would ne=
ed
several orders of magnitude more membrane area than the reverse osmosis
process, and therefore several orders more floor space in an installation, =
to
deliver treated water at a rate useful to the reverse osmosis system. However, the productivity of this syste=
m in a
large scale installation may deviate substantially from predictions made on=
the
basis of the laboratory scale data reported here. The continuous, high flow rate mode of
operation of a large scale system could show a significantly higher rate of
dilution than was observed here. An
industrial process based on this principle could reduce the costs associated
with SWRO, when there is ready access to comparable volumes of tertiary tre=
ated
waste water. Use of this type of p=
rocess
might be more acceptable in the production of drinking water, effectively f=
rom
recycled water. It would also remo=
ve the
environmental issues associated with RO concentrate disposal.
4.2. Compari=
son
of Observed Results with Theoretical Predictions
Figure 6. =
span>�Ideal9
and measured8 osmotic pressures of various concentrations of NaCl
solutions. The osmotic pressures of a variety of aqueous NaCl solutions can=
be
theoretically predicted using the van't Hoff equation and are compared with
values calculated from experimentally determined, published practical osmot=
ic
coefficient data8. Significant differences occur at concentratio=
ns
above about 3M, for aqueous NaCl solutions.
Figure 7. Experimental vapour transfer flux rates are compa=
red
with the calculated difference in vapour pressure between the two feed liqu=
ids. The rate of transfer of water through the hollow
fibre membranes has a direct linear relationship with the vapour pressure
difference between the two solutions8.� The equation of the trendline could be =
used
to predict the flow rate of the process for a known vapour pressure differe=
nce,
generated by any means, e.g. by application of a vacuum, by temperature
differential, or by osmotic pressure.
Careful comparison of Figs. 3, 5 and 6, shows that=
the
data from the osmotic distillation experiments seem to match the curve of t=
he
vapour pressure data more precisely than the osmotic pressure curve. This indicates that the kinetics of the
process is controlled by the vapour pressure differences across the membran=
es,
rather than the osmotic pressure, although the differences are slight. This is consistent with the mechanism o=
f the
process, and the broad fit of the data with the pressure curves, indicates =
that
the activity of the water is a reliable predictor of the rate of the vapour
transfer process.
The data used in Fig. 6 was derived from the pract=
ical
osmotic coefficients given by Colin et al8. For comparative
purposes, the osmotic pressures were also calculated using the published va=
pour
pressure data, from the same paper, by applying equation (9), and assuming =
that
<=
![endif]> is equal =
to the
molar volume of pure wáter.� The two sets of data that =
were
calculated agreed to 3 significant figures, indicating that the practical
osmotic coefficients were derived from vapour pressure values, and calculat=
ed
using the same assumption.
The use of hydrophobic membranes could be extended=
to
obtain direct measurements of osmotic pressures. As mentioned in the introduction, apply=
ing a
pressure to a liquid, against a hydrophobic membrane, results in an increas=
e in
vapour pressure on the other side of the membrane, due to the Kelvin
effect. If a hydrophobic membrane =
is
used to separate a solution with a known osmotic pressure, from one with an
unknown osmotic pressure, vapour will be transferred until the solvent
activities, and therefore osmotic pressures, are balanced. Vertical tubes connected to the solutio=
ns on
each side of the membrane and both open to the atmosphere, could simply be =
used
to measure any small difference in pressure between two closely matched
solutions, to measure small differences in osmotic pressure accurately.
Osmotic
pressures of solutions, or their osmotic coefficients, are usually determin=
ed
by measuring the vapour pressure of the solution, and converting to the osm=
otic
pressure using a relation, such as that shown in equation (9). This is because the osmotic pressure is
difficult to measure accurately, due to problems with slow equilibration ti=
mes,
variability between osmotic membranes, and membrane ion leakage. Directly
measuring the osmotic pressures of solutions using a hydrophobic membrane,
would allow a good test of theory. The
conversion from the vapour pressure to the osmotic pressure of a solution, =
or vice versa, requires accurate valu=
es for
the partial molar volume of water in the solution. However, the partial molar volume is
difficult to measure directly. Dir=
ect
measurement of the osmotic pressure, and comparison with the directly measu=
red
vapour pressure would allow the partial molar volume of water to be calcula=
ted
from equation (9). This method wou=
ld
also enable calculation of the partial molar volumes of the solutes.
5.� Conclusions
The low transfer flow rates observed with the
laboratory scale apparatus used in this study make the industrial applicabi=
lity
of this process to the treatment of a relatively low commercial value
commodity, such as water, an unfavourable proposition. However, comparable data from related s=
tudies
indicate that the process may be significantly improved, possibly to an ext=
ent
where it might become industrially useful. The results presented here may h=
elp
guide future studies into the development of these processes for the secure=
and
safe re-use of waste water. The results obtained in this study are consiste=
nt
with the trends predicted from vapour pressure data. Indeed, the results obtained here indic=
ate
that a suitable osmotic distillation process, or derivative of such a proce=
ss,
may be useful for measurements of thermodynamic quantities that are difficu=
lt
to obtain by other means.
Appendix
Nomencl=
ature
a������������ Act=
ivity
c������������ Con=
centration
(moles/m3)
l������������� Li=
quid
n������������ Num=
ber
(moles)
P����������� Pressure (Pa)
p������������ Vapour pressure =
(Pa)
R����������� Gas
constant (J/K mol)
r������������ Radius
(m)
T������������ Temperature
(K)
v������������ Vapour
phase
x������������ Mole
fraction
V����������� Volume
(m3)
Greek Symbols
����������� Surface
tension (N/m)
����������� Difference
����������� Contact
angle (�)
����������� Chemical potentia=
l
����������� Osmotic
pressure (Pa)
����������� Practical
osmotic coefficient
Superscripts
*
w
Subscripts
1,2
c
m
s
w
References
1. Pashley, R.M.; Karaman, M.E. Applied
Colloid and Surface Chemistry. J.Wiley &a=
mp;
Sons Ltd, UK, 2004.
2. Tai, M.S.L.; Chua, I; Li, K.; Ng, W.J.; Teo,
W.K. J.
Membr. Sci., 1994, 87(1-2),
99-105.
3. Wiesler, F. Ultrapure Water, March 2003, 38-42.<= o:p>
4. Rzechowicz, M; Pashley, R.M. J. Colloid Interface Sci., 2006, 298(1), 321-326=
5. Jiao, B.; Cassano, A.; Drioli, E.�
J. Food Eng. 2004, 63, 303�324.
6. Diban, N.; Athes, V.; Bes, M. J. Membr.=
Sci.<=
/i>,=
2008, 311(1-2), 136-1=
46.
7. Curcio, E.; Drioli, E. Sep. Purif. Rev.<=
/span>, 2005, 34, 35-86.
8. Colin, E.; Clarke, W.;
Glew, D.E.� J. Phys. Chem., 1985=
b>,
14(2), 489-610.
9. Wolf, A.V.; = Brown, M.G.; Prentiss, P.G. CRC Handbook of Chemistry and Physics 68th Edit= ion, R.C. Weast (ed.), 1988, CRC Pr= ess, pp D253-D254.��������������������� <= /span>
10. Robinson, R.A.�
Trans. R. Soc., N. Z. 1945, 75, 203�217.
�=
11. Partanen, J.I.;
Covington, A.K.� J. Chem. Eng. Data, 2009, 54, No. 2.
12. FilmtecTM Product Informat=
ion, Form No. 609-00377-0406, Dow,=
2008.
13. Fact Sheet, SWRO HR
Series, Form No. FS1289EN.doc Feb-09, General Electric Company, 2009.
14. Ander=
son, G.M.;
Crerar, D.A. Thermodynamics in
geochemistry: the equilibrium model, 1993,
Page 215.� Oxford University Press,=
UK.
15. Perron, G.; Roux, A.; Desnoyers, J.E. Can. J. Chem., 1981, 59, 3049-3054.
16. Garcia-Castello, E.M.; McCutcheon, J.R.; Elimelech, M. �J.
Membr. Sci., 2009, 338(1-2), 61-66.
17. B�lafi-Bak�, K.; Koroknai, B.� J. Membr.
Sci., 2006, 269, 187�193.
1=
8. Herron,
J.R.; Beaudry, E.G.; Jochums, C.E.; Medina, L.E. US Patent No. 5,281,430 (1994).
All Res. J. Chem, 2011, 2, 1-10
������������������������������������������������=
��
Issue 1, Volume 2, 2011=
, 1-10
������������������������������������������������=
��
All Res. J. Chem, 2011,=
2, 1-10
Refbacks
- There are currently no refbacks.
This website is optimized for the last versions of Internet Explorer (V. 7 or higher) and Firefox. We therefore advise to download (or upgrade your internet browser to) IE 7 or Firefox. All rights reserved to The All Results Journals (c).
To help promote The All Results Journals:Chem (ISSN: 2172-4563) you can now download our poster and display it in your library, common room, office or laboratory.
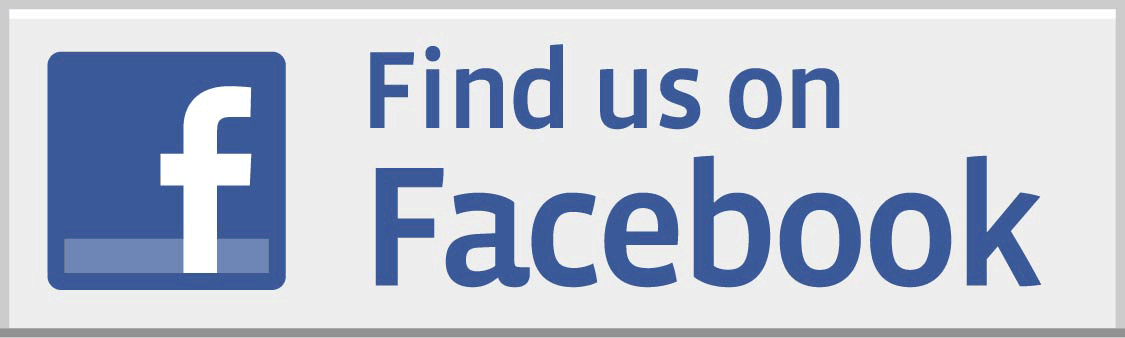
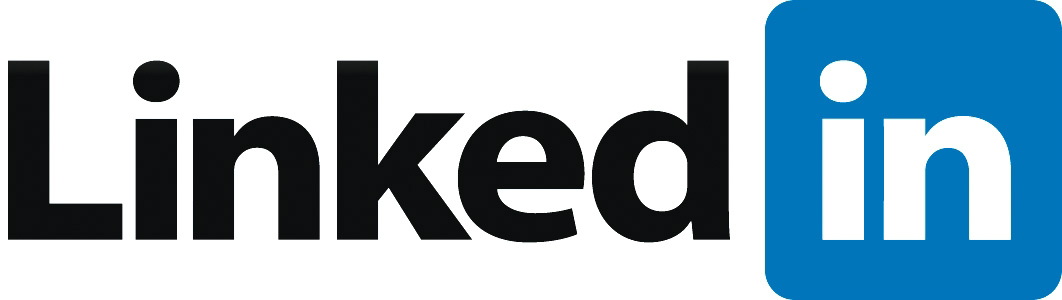